Nettoyage industriel : exemple de bonnes pratiques pour protéger la santé et la sécurité des salariés
Le secteur du nettoyage industriel étant particulièrement exposé aux risques d’accidents du travail ou de maladies professionnelles, l’entreprise Safetykleen a choisi de faire évoluer sa politique de prévention afin de mieux connaître les situations dangereuses, et donc de mieux anticiper les risques.
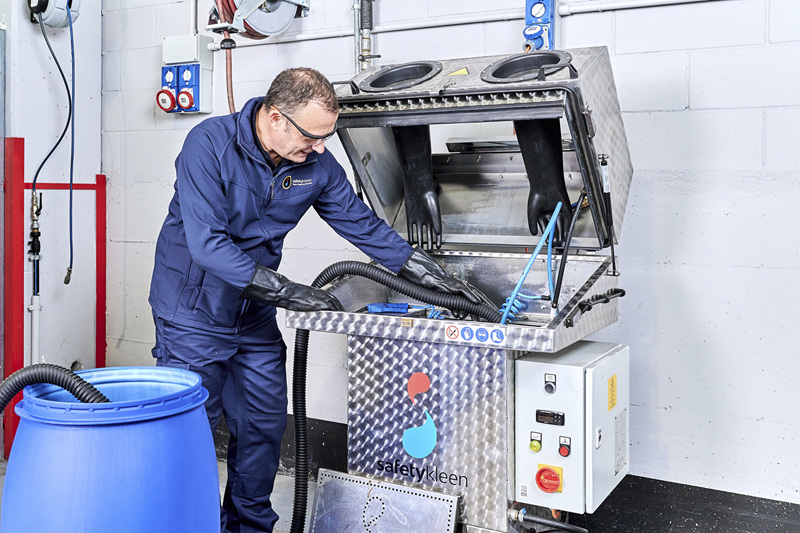
L’entreprise de nettoyage industriel Safetykleen a entamé une transition afin de remplacer les produits à base de solvants et de soude caustique, utilisés par l’industrie, par des formules lessivielles et aqueuses. L’objectif est d’éviter que les salariés soient exposés aux composés organiques volatils (COV) qui peuvent avoir des “effets cancérigènes ou toxiques pour la reproduction et le développement de l’être humain”, selon des données présentes sur le site de l’observatoire de la qualité de l’air en Île-de-France. Compte tenu de son secteur d’activités, Safetykleen est exposée aux risques pour la santé et la sécurité de ses employés. En 2010, l’entreprise a connu un accident dramatique : un de ses salariés est mort brûlé vif lors d’un accident du travail sur un site proche de Toulouse. La société, qui a été condamnée en 2019 à 50 000 euros d’amende pour ce décès, a depuis fait évoluer ses processus de sécurité. Robert Ledoux, manager qualité-santé-environnement (QSE) pour la France et le Benelux au sein de Safetykleen, a accepté d’en discuter avec Face au Risque.
Face au Risque : Qu’est-ce qui a été fait chez Safetykleen ces dernières années pour améliorer la santé et la sécurité des salariés ?
Robert Ledoux. Je suis arrivé il y a un an chez Safetykleen. Pour moi c’était un challenge de mettre en place d’une part des bonnes pratiques, et surtout, d’autre part, des moyens de prévention en complément de ce qui avait déjà été mis en place par mon prédécesseur et notamment l’obtention de la certification ISO45001 en 2021. Nous menons donc une politique d’évaluation des risques afin de prévenir les accidents. Nous travaillons sur la courbe de Bradley et sur la pyramide de Bird, et les salariés peuvent nous faire remonter les situations dangereuses. Et il y en a encore sur les sites. Par exemple, il y a parfois de la co-activité, avec des véhicules qui circulent alors que, dans le même temps, d’autres activités sont menées. Pour éviter les accidents, on met alors en place des plans de circulation.
Vous avez une politique visant à éviter les accidents liés à des chutes. Pouvez-vous nous en dire plus ?
R. L. Pour tout ce qui concerne les chutes, la configuration de nos sites fait qu’on s’attache à mettre en particulier certains risques en avant. Toutes les formes de chute sont évaluées en priorité, avec des consignes précises, et des modes opératoires précis. Par exemple, lorsque les salariés doivent utiliser des hayons sur les fourgons, nous avons un mode opératoire écrit qui précise comment ils doivent s’y prendre : il est interdit de sauter du hayon, de rouler avec un hayon ouvert, etc. Nous communiquons régulièrement auprès des salariés sur ces procédures de sécurité.
Avez-vous une politique spécifique visant à éviter les troubles musculo-squelettiques (TMS) ?
R. L. Oui. Dans le cadre du chargement et du déchargement des véhicules, nos salariés sont susceptibles de manipuler des fûts pouvant aller jusqu’à 200 kilos. Ils sont donc équipés de diables pour éviter d’avoir à porter tout le poids de ces fûts. Nous avons aussi pour objectif de mettre en place des transpalettes électriques pour limiter l’effort. C’est en test actuellement dans plusieurs centres.
Vous mettez en avant votre politique visant à limiter l’usage de produits à base de solvants et de soude caustique dans l’industrie. Où en êtes-vous de cet objectif, et par quoi remplacez-vous ces produits ?
R. L. Aujourd’hui, les produits à base de solvant représentent 10% des produits que nous fournissons, contre 50 à 60% il y a quelques années. Nous avons un service chimie qui étudie toutes les possibilités de substitution. Nous utilisons notamment des produits lessiviels de type non solvantés. Notre démarche reste la réduction des risques de santé pour les salariés.
Est-ce que cet arrêt de l’usage de produits à base de solvant a entraîné une baisse de productivité ou une hausse des coûts ?
R. L. Une hausse des coûts pour Safetykleen, oui. Les produits lessiviels que nous proposons désormais sont plus chers, car ils sont conçus afin de limiter les risques liés aux solvants tout en maintenant la meilleure performance de nettoyage, et ils nécessitent l’utilisation de beaucoup d’eau. En effet, ils sont dilués avec de l’eau osmosée, ce qui nécessite des installations plus coûteuses. Cette évolution est absorbée par Safetykleen car notre mission est d’offrir les solutions les plus efficaces à nos clients au meilleur prix.
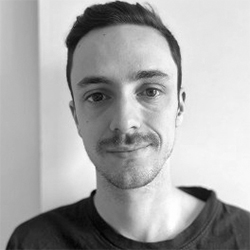
Camille Hostin – Journaliste
Les plus lus…
Le règlement européen révisé sur les produits de construction (EU CPR 2024/3110) est officiellement entré en vigueur le 7 janvier…
Les directives européennes NIS2 et REC doivent prochainement être transposées dans le droit français. Fabricants d’équipements de sécurité physique,…
La directive (UE) 2025/794 du Parlement européen et du Conseil du 14 avril 2025 est venue modifier les dates…
Deux arrêtés en date du 27 mars 2025 concernent les deux filières à responsabilité élargie du producteur (REP) « batteries…
Toute l’équipe de Face au Risque est ravie d’annoncer qu’elle a remporté la Victoire du design graphique pour son…
Le Conseil national des activités privées de sécurité (Cnaps) a confirmé, le 10 avril 2025, à l’issue d’un recours gracieux,…